1. 理論的なテストと分析
3つのうちタイヤバルブ会社から提供されたサンプル、2 つはバルブ、1 つは未使用のバルブです。A と B では、使用されていないバルブは灰色でマークされます。総合図 1. バルブ A の外表面は浅く、バルブ B の外表面は表面、バルブ C の外表面は表面、バルブ C の外表面は表面です。バルブ A と B は腐食生成物で覆われています。バルブA、Bの屈曲部に亀裂があり、屈曲部の外側がバルブに沿っており、バルブリング口Bが先端に向かって亀裂があり、バルブA表面の亀裂面の間に白い矢印が記されています。 。上から、亀裂はいたるところにあり、亀裂は最大であり、亀裂はあらゆるところにあります。
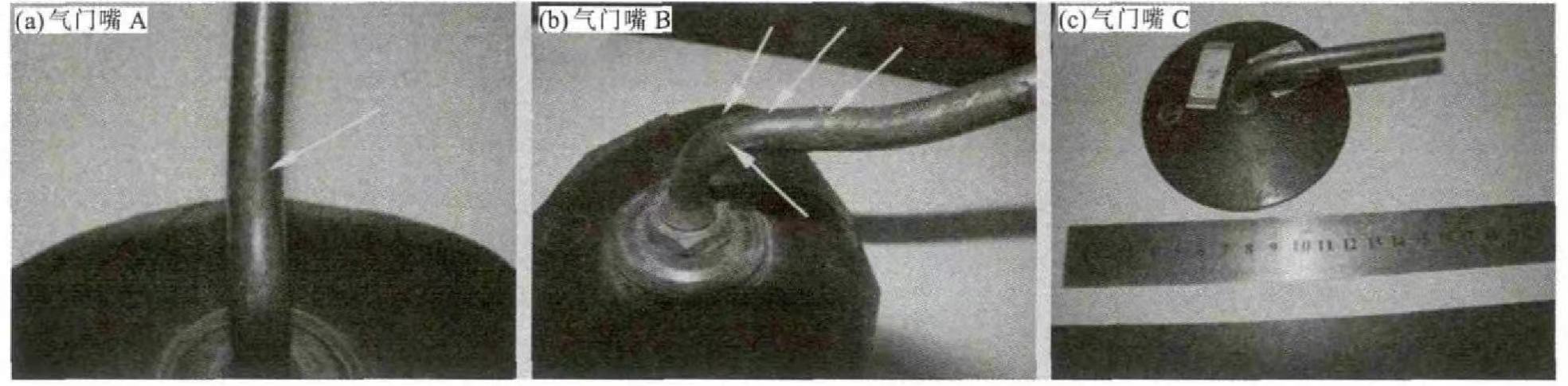
のセクションタイヤバルブA、B、C のサンプルを曲げ部から切り出し、ZEISS-SUPRA55 走査型電子顕微鏡で表面形態を観察し、EDS で微小領域の組成を分析しました。図2(a)はバルブB表面の微細構造を示しています。表面には白く明るい粒子(図中白矢印)が多く存在しており、この白色粒子のEDS分析ではS含有量が高いことがわかります。 白色粒子のエネルギースペクトル分析結果図 2(b) に示します。
図 2 (c) および (e) はバルブ B の表面微細構造です。図 2 (c) から、表面はほぼ完全に腐食生成物で覆われており、エネルギースペクトル分析により腐食生成物の腐食元素が確認できます。主にS、Cl、Oが含まれており、各位置のSの含有量が多くなり、エネルギースペクトル分析結果を図2(d)に示します。図 2(e) から、バルブ A の表面のバルブ リングに沿って微小な亀裂があることがわかります。図 2(f) および (g) はバルブ C の表面の微細形態であり、表面も同様です。完全に腐食生成物で覆われており、図 2(e) と同様に、腐食性元素には S、Cl、O も含まれます。亀裂の原因は、バルブ表面の腐食生成物分析からの応力腐食亀裂 (SCC) である可能性があります。図 2(h) もバルブ C の表面微細構造です。表面は比較的きれいで、EDS によって分析された表面の化学組成は銅合金の化学組成と類似していることがわかり、バルブが腐食していない。3 つのバルブ表面の顕微鏡的な形態と化学組成を比較することにより、周囲環境に S、O、Cl などの腐食性媒体が存在することがわかります。
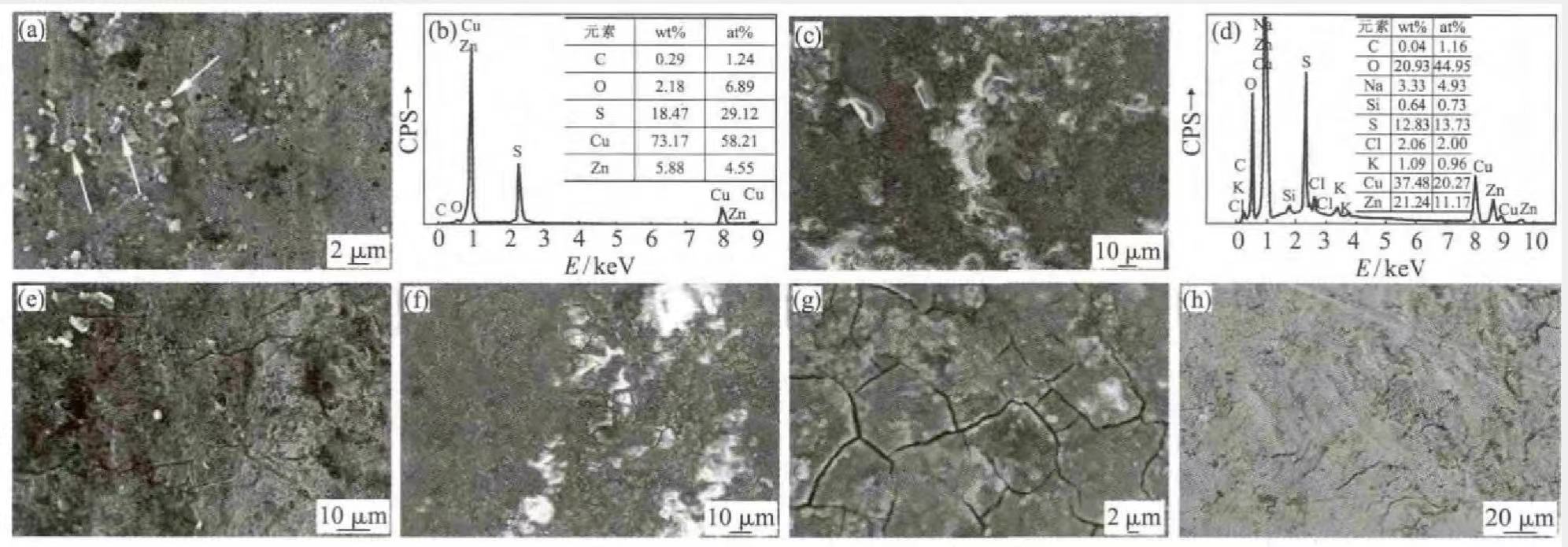
バルブBの亀裂は曲げ試験により開いたが、亀裂はバルブ断面全体に貫通しておらず、バックベンド側で亀裂が発生し、バックベンドと反対側では亀裂が発生していないことが判明した。バルブの。亀裂を目視検査すると、亀裂の色が暗く、亀裂が腐食していることがわかります。また、亀裂の一部の部分の色が暗く、これらの部分の腐食がより深刻であることがわかります。図 3 に示すように、弁 B の破損を走査型電子顕微鏡で観察しました。図 3 (a) は、弁 B の破損の巨視的外観を示しています。バルブ近くの外側の亀裂が腐食生成物で覆われていることがわかり、これも周囲環境に腐食性媒体が存在することを示しています。エネルギースペクトル分析によれば、図3(b)に示すように、腐食生成物の化学成分は主にS、Cl、Oであり、SとOの含有量が比較的多いことが分かります。破断面を観察すると、結晶型に沿った亀裂の進展パターンが見られます。図 3(c) に示すように、破面を高倍率で観察すると、多数の二次亀裂も確認できます。二次亀裂は図中の白い矢印で示されています。破面上の腐食生成物と亀裂の成長パターンも応力腐食割れの特徴を示しています。
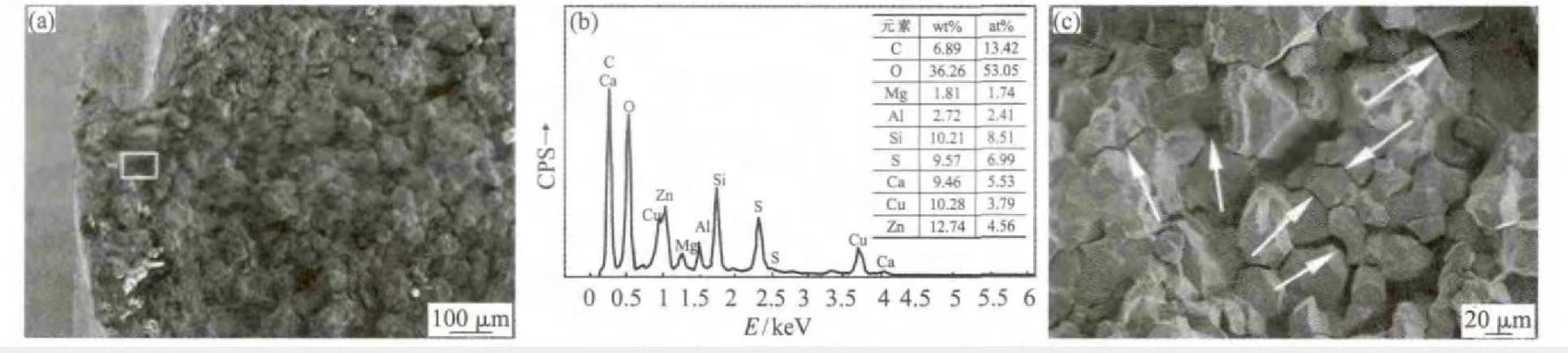
バルブ A の破断部が開いていないため、バルブの一部 (亀裂位置を含む) を除去し、バルブの軸方向の断面を研削および研磨し、Fe Cl3 (5 g) + HCl (50 mL) + C2H5OH ( 100mL)の溶液をエッチングし、金属組織および亀裂成長形態をZeiss Axio Observer A1m光学顕微鏡で観察した。図4(a)はバルブの金属組織を示しており、α+β二相構造であり、βは比較的微細で粒状でα相マトリックス上に分布している。周方向き裂におけるき裂進展パターンを図 4(a)、(b)に示します。亀裂表面は腐食生成物で満たされているため、2 つの亀裂表面の間の隙間は広く、亀裂の進展パターンを区別することは困難です。分岐現象。この一次亀裂には多数の二次亀裂(図中白矢印)も観察され(図4(c)参照)、これらの二次亀裂は結晶粒に沿って伝播した。エッチングされたバルブサンプルをSEMで観察したところ、主亀裂と平行な他の位置に多数の微小亀裂が存在することが判明した。これらの微小亀裂は表面から発生し、バルブの内部まで拡大しました。亀裂は分岐しており、結晶粒に沿って伸びていました (図 4 (c)、(d) を参照)。この微小亀裂の環境や応力状態は主亀裂とほぼ同じであるため、主亀裂の進展形態も粒界であると推測でき、これはバルブBの破壊観察からも確認されています。この亀裂は、やはりバルブの応力腐食亀裂の特徴を示しています。
2. 分析と考察
以上をまとめると、バルブの損傷はSO2による応力腐食割れが原因であると推測できます。応力腐食割れは一般に次の 3 つの条件を満たす必要があります。(1) 応力腐食を受けやすい材料。(2) 銅合金に敏感な腐食性媒体。(3) 特定のストレス状態。
一般に、純粋な金属は応力腐食を受けず、すべての合金は程度は異なりますが応力腐食を受けやすいと考えられています。真鍮材料の場合、一般に二相構造の方が単相構造よりも応力腐食感受性が高いと考えられています。黄銅材料中のZn含有量が20%を超えると応力腐食感受性が高くなることが文献に報告されており、Zn含有量が多くなるほど応力腐食感受性も高くなる。この場合のガスノズルの金属組織はα+β二相合金であり、Zn含有量が約35%と20%をはるかに超えているため、応力腐食感受性が高く、応力に必要な材料条件を満たしています。腐食割れ。
黄銅材の場合、冷間加工変形後に歪取り焼鈍を行わないと、適切な応力条件や腐食環境下では応力腐食が発生します。応力腐食割れを引き起こす応力は一般に局所的な引張応力であり、適用応力または残留応力が考えられます。トラック用タイヤは膨張後、タイヤ内の高圧によりエアノズルの軸方向に引張応力が発生し、エアノズルに周方向の亀裂が発生します。タイヤの内圧によって生じる引張応力は、σ=p R/2t (p はタイヤの内圧、R はバルブの内径、t はバルブの肉厚) に従って簡単に計算できます。バルブ)。ただし、一般にタイヤの内圧によって発生する引張応力はそれほど大きくないため、残留応力の影響を考慮する必要があります。ガスノズルの亀裂発生位置はいずれも後曲げ部であり、後曲げ部の残留変形が大きく、残留引張応力が存在していることが明らかである。実際、多くの実用的な銅合金部品では、設計応力によって応力腐食割れが発生することはほとんどなく、そのほとんどは目に見えず無視されている残留応力によって発生します。この場合、バルブのバックベンドでは、タイヤの内圧によって発生する引張応力の方向と残留応力の方向が一致しており、これら 2 つの応力の重ね合わせが SCC の応力条件となります。 。
投稿日時: 2022 年 9 月 23 日