1. 理論的検証と分析
3つのタイヤバルブ会社から提供されたサンプルのうち、2つはバルブで、1つはまだ使用されていないバルブです。AとBについては、使用されていないバルブは灰色でマークされています。総合図1。バルブAの外面は浅く、バルブBの外面は表面、バルブCの外面は表面、バルブCの外面は表面です。バルブAとBは腐食生成物で覆われています。バルブAとBは曲げ部でひび割れており、曲げの外側はバルブに沿っており、バルブリングの口Bは端に向かってひび割れており、バルブAの表面のひび割れ面の間に白い矢印がマークされています。上から見ると、ひび割れは至る所にあり、ひび割れは最も大きく、ひび割れは至る所にあります。
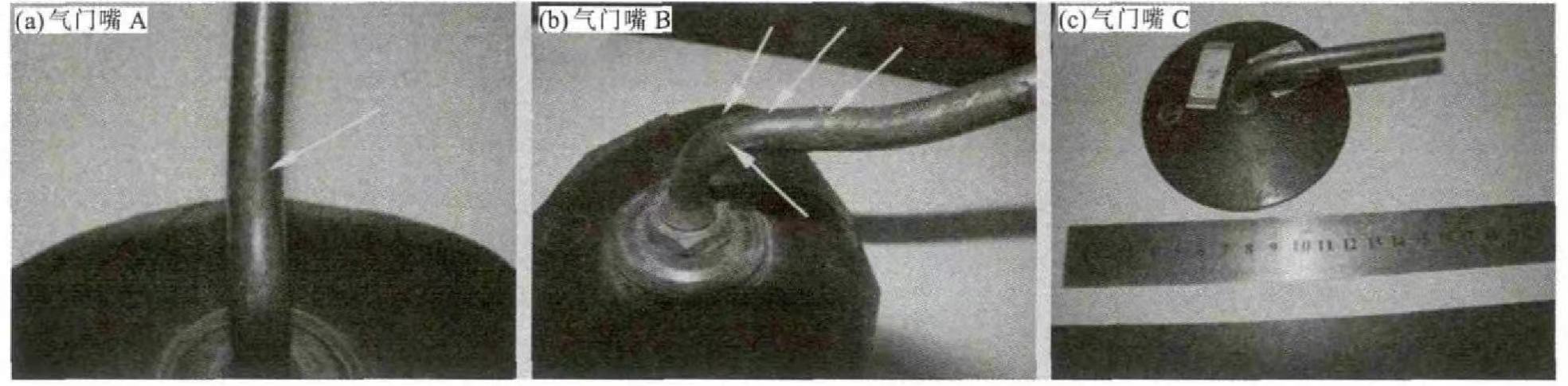
の一部タイヤバルブ曲げ部からA、B、Cのサンプルを切り出し、ZEISS-SUPRA55走査型電子顕微鏡で表面形態を観察し、EDSで微小領域の組成を分析した。図2(a)はバルブB表面の微細構造を示している。表面には白く明るい粒子が多数存在し(図中の白い矢印で示す)、白い粒子のEDS分析ではS含有量が高いことが分かる。白い粒子のエネルギースペクトル分析結果を図2(b)に示す。
図2(c)と(e)はバルブBの表面微細構造です。図2(c)から、表面はほぼ完全に腐食生成物で覆われていることがわかります。エネルギースペクトル分析による腐食生成物の腐食元素は主にS、Cl、Oであり、個々の位置でのSの含有量が高く、エネルギースペクトル分析結果は図2(d)に示されています。図2(e)から、バルブAの表面にはバルブリングに沿ってマイクロクラックがあることがわかります。図2(f)と(g)はバルブCの表面ミクロ形態で、表面も完全に腐食生成物で覆われており、腐食元素も図2(e)と同様にS、Cl、Oです。バルブ表面の腐食生成物の分析から、クラックの原因は応力腐食割れ(SCC)である可能性があります。図2(h)は、バルブCの表面微細構造です。表面は比較的清浄であり、EDS分析による表面の化学組成は銅合金の組成と類似しており、バルブが腐食していないことを示しています。3つのバルブ表面の微細構造と化学組成を比較すると、周囲環境にS、O、Clなどの腐食性媒体が存在することがわかります。
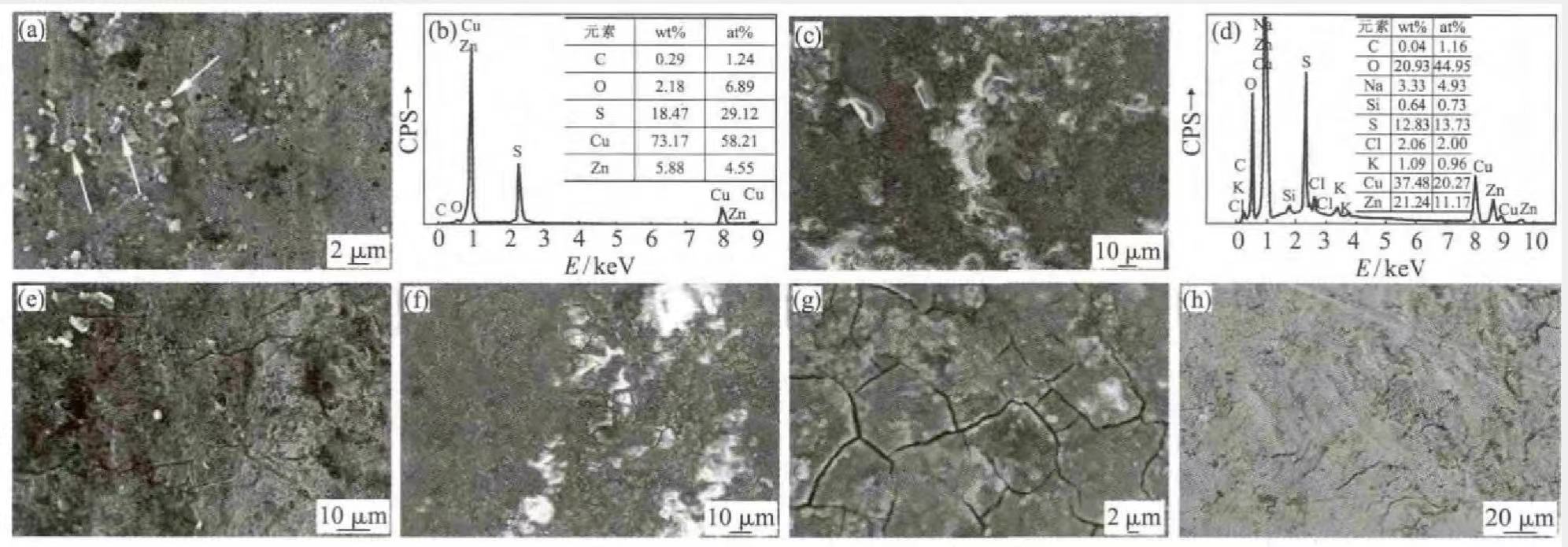
曲げ試験によりバルブBの亀裂が開口したが、亀裂はバルブ断面全体を貫通しておらず、バックベンド側で亀裂が発生し、バックベンドの反対側では亀裂が発生していないことがわかった。破断面を目視で観察すると、破断面の色が濃く、腐食が進行していることを示している。また、破断面の一部が黒く変色していることから、これらの部分では腐食がより深刻であることがわかる。図3に示すように、バルブBの破断面を走査型電子顕微鏡で観察した。図3(a)は、バルブBの破断面のマクロ的な外観を示している。バルブ近傍の外側の破断面が腐食生成物に覆われていることがわかり、これもまた周囲環境に腐食性媒体が存在することを示している。エネルギースペクトル分析によると、腐食生成物の化学成分は主にS、Cl、Oであり、図3(b)に示すように、SとOの含有量が比較的高い。破断面を観察すると、亀裂の成長パターンは結晶型に沿っていることがわかる。図3(c)に示すように、高倍率で破面を観察すると、多数の二次亀裂も確認できます。図では、二次亀裂は白い矢印で示されています。破面における腐食生成物と亀裂成長パターンは、応力腐食割れの特徴を示しています。
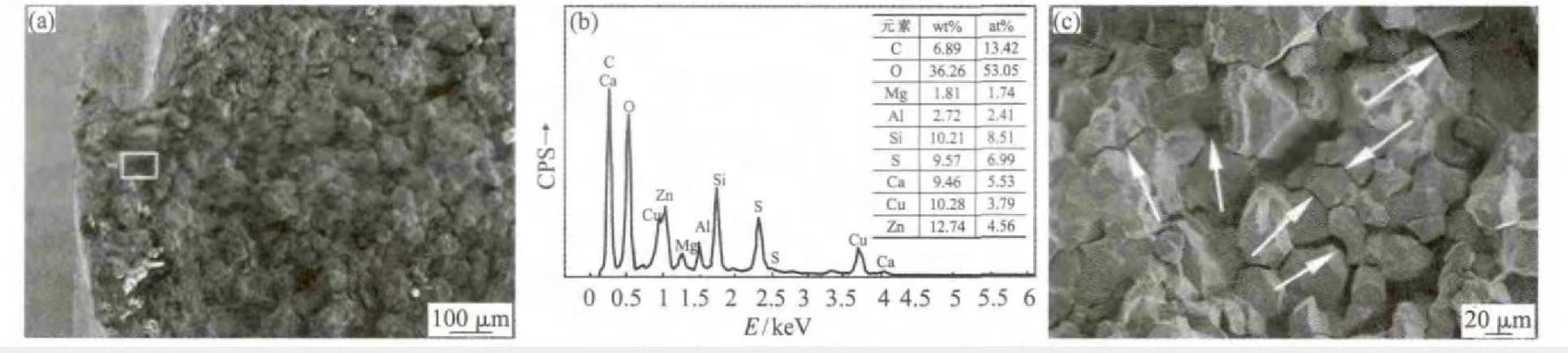
バルブAの破損部は開いていないため、バルブの一部(亀裂位置を含む)を切除し、バルブの軸方向部分を研磨し、Fe Cl3(5g)+HCl(50mL)+ C2H5OH(100mL)溶液でエッチングし、Zeiss Axio Observer A1m光学顕微鏡で金属組織と亀裂成長形態を観察しました。図4(a)は、バルブの金属組織を示しています。これはα+β二相構造であり、βは比較的細かく粒状で、α相マトリックス上に分布しています。円周亀裂における亀裂伝播パターンを図4(a)、(b)に示します。亀裂表面が腐食生成物で満たされているため、2つの亀裂表面間の隙間が広く、亀裂伝播パターンを区別することが困難です。分岐現象。この一次亀裂上には、多数の二次亀裂(図中白矢印)も観察され(図4(c)参照)、これらの二次亀裂は結晶粒に沿って伝播していた。エッチングされたバルブサンプルをSEMで観察したところ、主亀裂と平行な他の位置にも多数の微小亀裂があることが判明した。これらの微小亀裂は表面から発生し、バルブ内部へ拡大していた。亀裂は分岐しており、結晶粒に沿って延びていた(図4(c)、(d)参照)。これらの微小亀裂の環境と応力状態は主亀裂のものとほぼ同じであるため、主亀裂の伝播形態も粒界亀裂であると推論でき、これはバルブBの破壊観察によっても確認されている。亀裂の分岐現象は、バルブの応力腐食割れの特徴を再び示している。
2. 分析と議論
まとめると、バルブの損傷はSO2による応力腐食割れによって引き起こされたと推測できます。応力腐食割れは、一般的に3つの条件を満たす必要があります。(1) 応力腐食に敏感な材料、(2) 銅合金に敏感な腐食媒体、(3) 特定の応力条件。
一般に、純金属は応力腐食を受けないと考えられており、すべての合金は程度の差はあれ応力腐食の影響を受けます。黄銅材料の場合、二相構造は単相構造よりも応力腐食感受性が高いと一般的に考えられています。文献では、黄銅材料中のZn含有量が20%を超えると応力腐食感受性が高くなり、Zn含有量が多いほど応力腐食感受性が高くなることが報告されています。この場合のガスノズルの金属組織はα+β二相合金であり、Zn含有量は約35%で20%をはるかに超えているため、応力腐食感受性が高く、応力腐食割れに必要な材料条件を満たしています。
黄銅材の場合、冷間加工後に応力除去焼鈍処理を行わないと、適切な応力条件および腐食環境下では応力腐食が発生します。応力腐食割れの原因となる応力は、一般的に局所的な引張応力であり、これは外力応力または残留応力です。トラックタイヤに空気を充填すると、タイヤ内の高圧により、エアノズルの軸方向に沿って引張応力が発生し、エアノズルに円周方向の亀裂が発生します。タイヤの内圧によって発生する引張応力は、σ=p・R/2t(pはタイヤの内圧、Rはバルブの内径、tはバルブの肉厚)に従って簡単に計算できます。しかし、一般的に、タイヤの内圧によって発生する引張応力はそれほど大きくないため、残留応力の影響を考慮する必要があります。エアノズルの亀裂発生位置はすべてバックベンド部であり、バックベンド部の残留変形が大きく、そこに残留引張応力が存在することは明らかです。実際、多くの実用的な銅合金部品において、応力腐食割れは設計応力によって引き起こされることは稀で、ほとんどの場合、目に見えず無視される残留応力によって引き起こされます。この場合、バルブのバックベンド部では、タイヤの内圧によって発生する引張応力の方向と残留応力の方向が一致しており、これら2つの応力の重ね合わせがSCCの応力条件となります。
投稿日時: 2022年9月23日